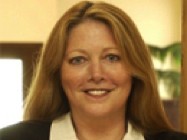
Sheila Dunn, D.A.
This is the third in a series of Featured Articles that cover OSHA compliance in the medical setting. In this article, contributing author Sheila Dunn, D.A. outlines tips for developing a culture of safety in your practice.
Your practice could be the target of an OSHA inspection – all because one employee (just one!) makes a complaint. It doesn’t matter what the complaint is about – grumbling about unsafe behavior, concern about a lack of safety policies – whatever the case, the whole situation can been avoided.
How? The key is to develop a culture of safety in your practice, from the top down. In other words, aim to make your organization a place where being safe is “the way things are done around here."
In the long run, not only will this approach help keep employees safe from workplace injury, it will minimize the threat of surprise visits by OSHA and save your practice money.
10 Tips for Developing a Safety Culture in Your Practice
For OSHA Safety Officers, developing a culture of safety doesn’t happen overnight, but it is possible. Following these tips will help:
- Add OSHA managerial duties to your job description. As OSHA Safety Officer, you need time to accomplish your duties, so it’s important that OSHA functions are specifically listed in your job description.
- Make sure everyone understands you wear the OSHA hat. Encourage staff to bring safety concerns to your attention. Be the go-to person for safety advice and leadership.
- Take all complaints seriously. Keep an open door and open mind to all safety concerns—even if you don’t think they’re justified. Employees often call OSHA when they feel management isn’t listening. Handle minor issues before they escalate into major problems.
- Document, document, document. At inspection time, if it wasn’t written down, it didn’t happen.
- Consider safety a “value,” rather than a “priority.” Business priorities change over time, but values endure. Since the needs or urgencies of the moment determine business priorities, safety cannot be guaranteed to be on the top of the list.
- Make safety compliance a requirement in each employee’s job description.
Discipline employees who purposely don’t comply. First, document the problem. Then speak personally with the employee. If the problem persists, document the incident and inform the supervisor. For serious cases, approach senior management and consider termination.
- Manage by walking around. This well-known management philosophy lets you find out whether employees are giving lip service to OSHA regulations or whether they’re actually complying.
- Make annual OSHA training applicable to your practice. Preview videos and identify areas where you can use examples from your practice to reinforce the material. Keep employees involved; have them voice opinions or demonstrate techniques.
- Keep your cool. Manage OSHA tasks using monthly and annual checklists to organize your duties. Listen to employee concerns, but don’t take safety related criticisms personally (“I hate that we have to use these safety needles”).
- Keep benefits of OSHA compliance in front of organizational leaders. Part of managing your practice’s OSHA safety program is quantifying its contribution to management. Sure, there are benefits: fewer injuries, less downtime, reduced workers’ comp claims, improved employee morale (minimizing the likelihood of that “one” complaint to OSHA).
Management will almost always be more responsive to numbers. Identify how workplace injuries and illnesses impact your facility. Include hidden costs like lost workdays, workers' compensation, and the expense of replacing a worker. Track these costs over time. Show your organization’s leaders how a stronger commitment to safety will reduce these expenses. If you can measure it, you can manage it. Helping management to understand the cost of unsafe practices is your ammunition in gaining its commitment to a safe workplace.
Strong leadership support and a focus on repetitive education, enforcement, and encouragement will lead to a real change in safety performance as a safety culture grows within your organization. This culture of safety will help to prevent suprise OSHA inspections.
About the Author:
Dr. Sheila Dunn, president and CEO of Quality America, Inc., holds a doctoral degree in clinical laboratory science.
Read more about medical OSHA compliance:
OSHA’s Medical Services First Aid Requirements: An Overview
Material Safety Data Sheets: An Overview